Posted by : John Eaton
10:35 AM
It appears that Bandai plans to do a special 50th Anniversary edition of the Popy/U5 Mazinger Z. This was spotted on the TagHobby website . ...
Read more »→
Posted by : John Eaton
4:10 PM
Back when I hosted SW.org on the Wildtoys site I had a separate section called "Toy Story" which provided personal memories rega...
Read more »→
Posted by : John Eaton
10:09 AM
I spent some time expanding each of the Collectors Shogun Warriors into their own pages with photos of packaging variations. Also updated th...
Read more »→
Posted by : John Eaton
12:45 PM
Ninja Kyaputā I realized that I was getting a bit repetitive in the various Shogun Warrior categories when referencing the source tokusats...
Read more »→

Jumbo Machinder News - Recent, Upcoming Releases and Pre-orders 2023
Jumbo MachindersMattel CreationsMOTUNew ReleasesSuper7Toynami
Posted by : John Eaton
11:43 AM
There are a few releases planned for 2023 - some of these were originally announced years ago. I thought I'd do a general post about ...
Read more »→
Posted by : John Eaton
6:13 PM
Put a couple of new pages up... Shima X Dragon Boy Mechasaurus Doba Garada K7 That Doba is really fantastic...
Read more »→
Posted by : John Eaton
8:34 PM
The Danguard Gang Was able to create pages for: Popy Danguard Ace 1977 Jumbo Machinder Peru Danguard Ace Knock-off Jumbo Machinders I hop...
Read more »→
Posted by : John Eaton
1:39 PM
A few new pages including Goldwell Daitarn III https://www.shogunwarriors.org/p/goldwell-daitarn-3.html and a new Takemi Page https://ww...
Read more »→
Posted by : John Eaton
10:12 AM
Super Shogun Optimus Prime After many delays, presumably due to the Pandemic, the Super 7 release of the Super Shogun Optimus Prime has sh...
Read more »→
Posted by : John Eaton
11:00 PM
Shogunwarrior.com updates! Added a new page: https://www.shogunwarriors.org/p/god-mars.html Also updated the Customs page: https:/...
Read more »→
Subscribe to:
Posts (Atom)
Labels
- Jumbo Machinders
- Popy
- Updates
- Shogun Warriors
- Mattel
- Popy Accesssories
- Super7
- Bandai
- Customs
- Nakajima
- Paper Items
- Shogun Warriors Action Vehicles
- Toynami
- Collecting
- Combatra
- Dragon Boy
- Godzilla
- Mandarake
- New Toys
- Power Rangers
- Raydeen
- Restoration
- Sentai
- Shogun Warriors Action Figures
- Unifive
- Variations
- Announcement
- Bootleg
- Clover
- Colorforms
- Cosplay
- DIY
- Daimos
- Danguard Ace
- Famosa
- Funko
- Gojira
- Great Mazinger
- Jugarama
- Jumbozaurus
- Kaiju
- Kikaju
- LJN
- MOTU
- Marmit
- Marvel Comics
- Mattel Creations
- Mazinga
- Memories
- Migration
- Mini-Machinder
- Misc
- Model Kits
- Monogram
- New Releases
- Raideen
- Shipping
- Shogun Warriors Action
- Stickers
- Takemi
- Toy Show Report
- Toy Story
- Transformers
- Vintage Photos
- Voltron
- Whitman
Popular Posts
-
It appears that Bandai plans to do a special 50th Anniversary edition of the Popy/U5 Mazinger Z. This was spotted on the TagHobby website . ...
-
I've had a few newcomers to the hobby ask for some advice on how to start collecting Shogun Warriors toys, so I thought I would sha...
-
Recently there have been several ads on eBay regarding the repair of the Godzilla Lever - the red stick protruding from the back of the...
-
What's in a Fist? When I first started collecting Shogun Warriors it quickly became apparent that there were different versions of...
-
Original Tetsujin 28 Sticker Sheet I've had a few people ask me about replacement stickers so I thought I would cover those. All S...
About Me
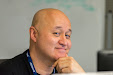
- John Eaton
- I've been writing about stuff that interests me for many years, initially with some free web space provided by my ISP back in the 90's and continuing with various blogs and websites today, separated by interest. Many I haven't touched in a few years due to time constraints but the subjects are still on my mind.